What is UV Lithography and Why is it Important to Your Business?
This article will explain what UV lithography is and why it is important to your business. It uses lasers to produce light with a wavelength of 13.5 nanometers. This technology is capable of reducing the size of microprocessors by as much as five to ten times. It can produce detailed designs that can be easily transferred to other parts of the same microprocessor. In this article, we will also explain what EUV lithography is and how it works.
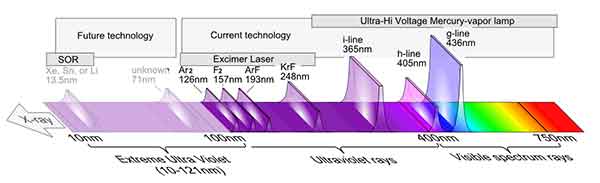
EUV lithography produces light of a wavelength of 13.5 nm
EUV lithography is a fabrication method that produces light with a 13.5-nm wavelength, which is short enough to produce large features on a chip. It is widely used in the manufacturing of next-generation chips, and is planned by Intel to be used to make processors in the future. Its advantages include cost, simplicity, and speed. Here are some advantages of EUV lithography.
The generation of EUV light is a complex process that has limited success, but a division of ASML is developing new technologies to make it easier to generate this wavelength. The company has designed new EUV sources based on laser produced plasma (LPP) technology, which will produce 13.5-nm light. LPP technology creates an ionized gas plasma with electron temperatures of several tens of electron volts. EUV radiation is then collected by a special 0.5-meter mirror coated with layers of silicon and molybdenum. The light is then directed into the Intermediate Focus position.
Research on EUV lithography began in the 1980s, but the first successful applications began in the 1990s. In 1994, a coalition of semiconductor industry companies delivered the first prototype and proved its viability. The industry accelerated its development, and today the technology is in widespread use. In fact, it is expected to be an important part of the manufacturing process for semiconductor chips.
The use of EUV lithography is extremely complicated, requiring new mask infrastructure and step-and-scan systems to produce semiconductor chips. The technology is difficult to use, and the resolution can sometimes fall short of expectations. EUV lithography is an ideal choice for next-generation chip applications. With its shorter wavelength, it can print nanometer-scale features on wafers.
It reduces the size of microprocessors by five to ten times
Ultraviolet (UV) lithography is a technique for making semiconductors that reduces the size of microprocessors five to ten times. This technology uses UV light to carve transistors into silicon wafers. It is capable of making microprocessors with speeds up to 100 times faster than today's fastest chips and memory chips with similar increases in storage capacity.
The wavelength of ultraviolet light is 13.5 nanometers, which is similar to x-rays. Because it is more difficult to process photoresists that are used in UV Lithography, chip designers had to change their designs. Eventually, they resorted to multiple patterning, which allowed them to make microprocessors with finer features.
Another crucial part of the lithography process is a glass-and-metal module. The module will carry patterns for the microchip. Then, a machine will blast it with extreme ultraviolet light. This light will illuminate various parts of the chip pattern and bounce down to a dinner-plate-sized silicon wafer, burning the pattern into place. It is a complicated process, but it's one that will be a big game changer in the chip industry.
While it took years for ASML to realize the benefits of UV Lithography, it has managed to defy predictions that the technology would fail to deliver a substantial return on investment. In its first year of commercial production, the company produced microprocessors with an estimated five to ten times smaller footprints than today's processors. It is expected to be in mass production by 2020.
The technology is not without its limitations, however. The chip industry will run into physical limitations soon, and quantum problems will be emerging. However, a few tricks that have been used to keep deep UV machines going will still hold. The EUV machines will allow chipmakers to achieve even more tiny microprocessors. But the EUV will require more advanced techniques. The technology is not without its risks, but the potential benefits far outweigh the drawbacks.
It has high resolution
UV Lithography is a process for fabricating electronic and photonic components with high resolution and quality. The process uses ultraviolet light to transfer the pattern onto a surface. This method is highly versatile and low-cost. This process can be combined with etching processes to create metallic structures. It has been widely used for the production of semiconductors and optical devices. UV Lithography has high resolution, but the flexibility is limited by the necessity of precise molds.
The most commonly used wavelength for UV lithography is 250 nm. However, as the resolution of semiconductor devices increases, the wavelength must be increased. The wavelength of the UV light varies depending on the material being processed, which leads to the shift of line ends. The process also faces challenges in maintaining high throughput due to reduced fields, increased mirrors, and shot noise. To overcome these challenges, UV Lithography requires high power at the intermediate focus.
EUVL has a high resolution compared to deep UV lithography. However, there is an issue with EUVL in terms of the resolution. Its resolution is determined by the interaction volume between the EUV and the photoresist, as the EUV emits low energy electrons that may blur the original image. In addition, EUVL requires a vacuum chamber and all optical elements must be defect-free Mo/Si multilayers. These multilayers are comprised of 40 Mo/Si bilayers.
Current state-of-the-art photolithography tools use deep ultraviolet light (DUV) at wavelengths of 248 and 193 nm. With these tools, the minimum feature size for high-resolution lithography is about 50 nm. However, this depth of focus limits the depth of the photoresist and topography. For this reason, chemical mechanical polishing is often used to flatten the topography of the photoresist before the high-resolution lithography steps.
It uses lasers
UV Lithography is a method for creating high-resolution images of nanoelectronic devices. Lasers of the ultraviolet spectrum, with a wavelength of about 400 nm, are used to create intricate patterns. While it is still in its infancy, EUV lithography promises to advance world and electronics technology. While it is currently quite expensive, the process will become more affordable as laser power and cooling efficiency improves.
This method utilizes lasers to create micro and nano structures on photoresist or other photosensitive material. Laser characteristics, such as wavelength, power, and stability, play an important role in the economics of this process. A higher power, for example, translates to higher throughput, a lower cost per image, and a longer lifetime means less downtime and operating expenses. Cymer Inc., a subsidiary of ASML, produces the lasers needed for UV Lithography.
EUV lasers have numerous benefits and are more efficient than deep UV. They are used to manufacture chip-scale transistors. As a result, they can produce features that are less than 280 nm. Further, EUV lasers are smaller than deep UV and are therefore more effective for producing small features. EUV technology also allows for the production of large chips, which is essential for the manufacture of smartphones. And the future of the process is EUV.
The process is complex, involving a sophisticated optical system, which involves a complex array of nearly forty thousand optical lenses. The light is filtered before leaving the source vessel and reaching the scanner unit. Once the radiation reaches the surface of a microchip, it is then transferred to the target object using UV Lithography. It is also widely used in other fields. In the near future, the technology will allow a wide range of applications, including making microchips for the aerospace industry.
It is used to manufacture microprocessors
Extreme ultraviolet lithography is a cutting-edge fabrication process that uses extremely short wavelengths of light to create complex, detailed circuits. It is widely used in the manufacturing of memory chips and storage capacity in semiconductors. Its future is unknown, but growth is expected to be rapid over the next five years. This technology is expected to become increasingly popular with smartphone makers due to its ability to reduce cost, complexity, and power consumption.
This process is particularly useful for the manufacture of microprocessors, as the wavelength is so small that it cannot be focused using lenses or mirrors. However, modern techniques can use excimer laser lithography to produce features that are a fraction of the wavelength of light used. These new techniques can be highly sensitive and produce features with dimensions fractional to the wavelength of light used. This technique is expected to be used in mass production by 2020.
The EUV process uses a laser with a wavelength of 13.5 nanometers, which is smaller than deep UV and is suitable for manufacturing chip-scale transistors. The EUV process is easier to control than deep UV and has less downtime. Once it becomes scalable, it will cost less to produce the same amount of chips. In the meantime, manufacturers will need to convert their deep UV plants into EUV-only facilities. In the long run, however, the EUV process will make the manufacturing of microprocessors much cheaper.
The development of EUV lithography has helped manufacturers create smaller processors, which could be even smaller than the 28nm limit. Currently, the depth of the ultraviolet wavelength used for etching chip circuitry is 193nm. It is expected to reach that limit in five years, so chipmakers will need to develop other technologies to extend the life of silicon. The development of EUV light is being aggressively pursued by companies like ASML.