Indium-Tin-Oxide (ITO) Coated Substrates For Ellipsometric Research
Typical researchers quote request:
We woulk like to have silicon wafers coated with
indium tin oxide. We would like a thin coating that is tansparent and conductive at the same time. We will use this coated wafer for ellipsometric studies. I was wondering if you can provide us with such coatings?
Reference #100034 for specs and pricing.
Buy ITO Substrates Online and Save!
Indium Tin Oxide Substrates to Study Deformable Mirror for Adaptive Optics Applications
A university scientist requested a quote for the following:
I'm conducting a research that requires the use of some photoconductors, and I would like to ask if it would be possible to have a layer of indium tin oxide (ITO) deposited on one side of the wafer.
I am working on a device used as deformable mirror for adaptive optics applications. I am in the very early phase of my work, and my goal now is to gain experience with assembly and understand the process problems that can arise. For now I am looking for few materials to test, and they are: silicon, gallium arsenide and zinc selenide. The requirements are: high resistivity, thickness not higher than 3 millimeters, round shape, lapped on both sides, and as already mentioned if it was possible to lay a layer of ITO.
Reference #246503 for specs and pricing.
Get your Indium Tin Oxide (ITO) Glass Wafer Quote FAST!
What is Indium Tin Oxide on Glass?
Indium tin oxide (ITO) on glass substrates refers to a thin film coating that combines indium oxide (In2O3) and tin oxide (SnO2) deposited onto a glass surface. It is commonly used in various electronic devices, such as flat-panel displays, touchscreens, and solar cells.
ITO is highly transparent to visible light, making it suitable for applications that require transparency, like displays. Additionally, it has good electrical conductivity, enabling it to function as a transparent conductor. This property is crucial for touch-sensitive screens where electrical signals must pass through the transparent layer to detect touch input.
The deposition process for ITO involves techniques like physical vapor deposition (PVD) or sputtering, where a target consisting of indium and tin is bombarded with ions in a vacuum chamber. This results in the ejection of atoms from the target, which then condense onto the glass substrate, forming a thin, uniform layer of ITO.
ITO-coated glass substrates offer a balance between optical transparency and electrical conductivity, making them ideal for applications where both properties are essential. By applying a voltage to the ITO layer, the conductivity allows for the flow of electrical current while still permitting light transmission.
It's worth noting that while ITO has been widely used, there is ongoing research to explore alternative transparent conductive materials that could potentially replace ITO due to its scarcity and brittleness.
ITO Glass for Resistive Anode Detector
A physics and astronomy Ph.D student asked the following:
Question:
I'm reaching out to you regarding ITO Glass squares I've seen on your site. I would be interested in potentially incorporating these into a resistive anode detector, but would want to know what the porosity of the material is to know if it would be suitable in our vacuum conditions. Would you have any information on this?
15-20 ohm/sq ITO glass Size: 100mm x 100mm Please specify thickness from 1.1 or 0.7mm
Qty 10
Answer:
ITO layer is deposited via high vacuum sputtering at elevated temperature. Very stable under any vacuum.
No porosity.
Reference #273659 for specs and pricing.
At What Temperature Do ITO Glass Wafers Start Degrading?
A Phd candidate asked for the following quote:
"ITO Glass take a temp of more than 90C?"
Indium tin oxide (ITO) glass can withstand temperatures up to around 200°C, but its electrical and optical properties can degrade above 90°C. The exact temperature limit for ITO glass depends on various factors such as the composition, thickness, and deposition process, among others. It is best to consult the manufacturer's specifications for more information on the temperature tolerance of a specific ITO glass product.
Reference #272563 for specs and pricing.
ITO glass Specifications
Product configuration
Glass / SiO2 buffer (~23 nm) / ITO
ITO coating
Magnetron sputtering
ITO patterning
Photolithography
Size
Any size up to 14â€x 16â€
Typical sheet resistance
(ohm/sq)
6, 10, 13, 15, 20, 60, 100, 250, etc
(Others are also available for volume production)
Substrate thickness (mm)
0.4, 0.55, 0.7, and 1.1
Pre-patterned
Via photofilm or Cr mask
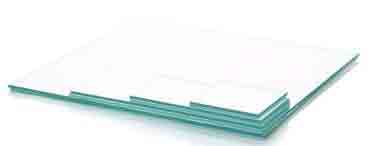
ITO plastic film
Specifications
Product configuration
Polyethylene terephthalate (PET) / ITO
PEN / ITO
ITO coating
Magnetron sputtering
ITO patterning
Lithography / Screen-printing / Laser patterning
Size
Sheet / roll (width <=1200 mm)
Typical sheet resistance (ohm/sq)
6, 10, 14, 20, 50, 60, 80, 100,
120, 150, 250, 300, 350, 450, 500
Substrate thickness (mm)
0.125, 0.175, 0.188, 0.21
ITO Physical properties
ITO Work function
4.9 eV (UPS)
We offer consultation for ITO cleaning
4.8-4.9 eV (UPS)
(after exposed to Chloro-based solvents)
ITO thickness
Usually, up to 125 nm
Micro-roughness
RMS 1-2 nm (Digital Instrument 3100 AFM)
Optical transmission
> 85% at 555 nm.
Pilkington FTO glass (TEC series)
We can provide Pilkington TEC15 FTO glass to you. Please find the price as below:
15ohm/sq Pilkington FTO glass (TEC15)
Surface resistance: 12~14 ohm/sq
Thickness of glass: 3.2mm
Transmittance: >82%
Haze: <0.74%
Smoothness: N/A
Size: 50mm x 50mm x 3.2mm
Often used for solar applications.
Nippon Sheet Glass FTO
Specifications
FTO glass manufacturer
Nippon Sheet Glass Co. Ltd., Japan
300mm x 300mm
Typical sheet resistance (ohm/sq) < 7 and 13
Substrate
Soda lime float glass
Substrate thickness (mm)
2.2 and 3.1 +/- 0.2
Visible transmission > 77 %
Haze >8 %
Normal FTO glass
Specifications
FTO glass manufacturing
PRC
Size
Any size up to 300mm x 300mm
Typical sheet resistance (ohm/sq) <15
Substrate: Clear soda lime float glass
Substrate thickness
2.2 mm
Remark: Customer services including patterning are available. We can offer patterning service for your ITO substrates.
Indium Tin Oxide Material Explained
Indium Tin Oxide Coated Glass for Sale
MAIN PRODUCTS buy online and save!
- ITO coated glass
- ITO coated plastic film (PET, PEN, etc)
- Fluorine-tin-oxide FTO coated glass
- FPD and ITO glass detergents
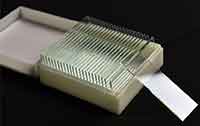
ITO Glass Sizes Inlcude But Not Limited To:
- 300mm x 400mm
- 400mm x 500mm
- 450mm x 550mm
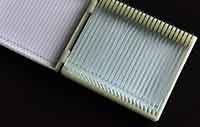
ITO Glass Slides Sizes
- 25mm x 25mm
- 25mm x 75mm
- 50mm x 75mm
We have the following Indium Tin Oxide wafers. Please let us know if any interest you. Or if you know of better pricing elsewhere!
< 10 ohm/sq ITO coated SiO2 wafer
Surface: Polished grade
Size: 4" dia. x 0.55mm
10 $65.90 each
25 $55.90 each
50 $47.90 each
100 $43.00 each
----------
<20 ohm/sq ITO coated SiO2 wafer
ITO thickness: ~ 100nm +/-10nm
Surface: Polished grade
Size: 4" dia. x 1.1mm
25 $34.90 each
50 $30.90 each
100 $25.90 each
----------
<20 ohm/sq ITO coated SiO2 wafer
ITO thickness: ~ 100nm +/-10nm
Surface: Polished grade
Size: 4" dia. x 0.7mm
25 $38.90 each
50 $34.90each
100 $30.90 each
----------
< 10 ohm/sq ITO coated SiO2 wafer
Surface: Polished grade
Size: 4" dia. x 1.1mm
25 $38.90 each
50 $34.90each
100 $30.90 each
----------
< 10 ohm/sq ITO coated SiO2 wafer
Surface: Polished grade
Size: 4" dia. x 0.7mm
25 $43.00 each
50 $38.90each
100 $34.90 each
----------
<7 ohm/sq ITO coated SiO2 wafer
Surface: Polished grade
Size: 4" dia. x 1.1mm
25 $43.00 each
50 $38.90each
100 $34.90 each
----------
<7 ohm/sq ITO coated SiO2 wafer
Surface: Polished grade
Size: 4" dia. x 0.7mm
25 $43.00 each
50 $38.90each
100 $34.90 each
----------
<7 ohm/sq ITO coated SiO2 wafer
Surface: Polished grade
Size: 4" dia. x 0.7mm
25 $51.90 each
50 $43.00 each
100 $38.90 each
ITO Coating Services on Silicon Wafer
A researcher requested the following:
I’d like to know if you provide coating services on silicon wafers? I am interested in coating Indium Tin Oxide (ITO) on one side of a wafer and a thin layer graphite on the other. Is there also alternative coatings for graphite? I am worried that the graphite strip off since it will be exposed to water. The particular wafer I’m interested in is Item 2950 which is undoped, D:100mm, T:50um, Grade: Prime, Float Zone. I would be interested in a quantity of 5 to be coated. Please let me know if that is possible or if you know who I can contact for the coating. Thank you for taking the time to look at my request. I will reply with more details and specifications if need be.
What I need to do is build a proof of concept which requires something that “activate” conductivity on different spots on a surface on demand. I have started initially with TFTs in a LCD assembly, but those are both complicated to obtain/manufacture and too much limiting in terms of current. Researching a bit more on TFT, Poly-Silicon/a-Si and everything related to how thin film transistors are made, I got curious about a different approach to my problem which is explained below.
Using the phototransistor concept, I figured I could use a silicon wafer to make conductive zones that I could use to pass current. Imagine a setup where a laser beam hits a small spot at the center of the wafer. Assume that the side on which the laser shines on is charged, say positively (enter the ITO coating, transparent and conductive). The cylindrical Silicon volume above the laser spot would become more conductive due to energy absorption, right? Then touching with a negative probe directly on the other side of the wafer would complete the circuit. If the probe is moved away from the center, this would result in a rapid decrease in current since it is dependent on the resistance. By that logic, there is only a limited spot on the probe side that is “activated”. Moving the laser spot would move the conductive spot per say. Now, there are many aspects I need to understand before committing to this proof of concept. I would really appreciate it if you looked at this setup and tell me if I’m in any way wrong in my understanding. I also have multiple questions regarding that:
- Is a P or N doped or undoped Silicon make a difference in the amount of current that can go through the wafer?
- I feel like using PN Junction(s) would only be useful if I want the current to be amplified. Is it necessary if I just need to check the resistance a difference spots? I’d like to test this setup and try to maximize current with only an undoped Si safer.
- I have read that when Silicon is exposed to air, it would oxidize up to a certain depth and become SiO2 which has a high resistance. Since I am interested in resistance through the thickness only, is this going to be a problem based on the fact that the oxidized layer is extremely small?
- If I replaced the oxidized layer with something more conductive, what is the point at which the “active” spot becomes too large? It is strongly dependent on layer thickness and resistance. I’m wondering what the best approach is… Does it even need this conductive layer? It’s the reason I am worried about using graphene oxide coating since it would make the whole surface conductive and render it useless.
- This conductive layer is going to be exposed to air and water and even acid environment. It’s the reason I was interested in graphite. The small SiO2 layer is going to be okay as long as it’s not an HF acid. Do you guys clean the wafers with this prior to applying any coating?
- If it works somewhat for laser printers, I think it would also have a chance to work in a flat shape? I’m thinking about the photosensitive drum which is basically a-Si.
I have many more questions and worries but I think this covers pretty well my short term intentions and uncertainties. I will understand if you don’t want to bother reading this long e-mail because this is probably not your problem, so I won’t take offense. Please understand that I’ve been working on this project for more than a year now and that I see a great potential and great applications. I tried contacting friends and professors who are knowledgeable in electrical engineering, and almost all of them simply didn’t have time or didn’t know the answers. Maybe I’m just bad at convincing people… Either way, I’ll be very grateful and as mentioned before I will definitely pay you back in some way for your help. Maybe even purchase more wafers if necessary or get stock from you that you can’t sell. Hope that this e-mail finds you well. Thank you for reading.
Refernce #228263 for specs and pricing of the following:
ITO coating service
30nm ITO
Sputtering
Size: 100mm dia. x 0.5mm
Graphite coating
We can do reduced graphene oxide coating.
ITO Glass Substates Used for Electroadhesion
A postdoctoral researcher developing sensors and actuators for robotics requested the followng quote:
I am a researcher scientist working on electroadhesion. I would like to know more about your thin film coating on ITO glass substrates. For my project, I need a thin (~0.5 mm) glass coated with ITO ideally with surface resistivity less than <10 ohm/sq. And I additionally need a thin insulation layer on the ITO, i.e., dielectric layer with a thickness <1um. So my structure will be Glass + ITO + dielectric. The dielectric layer will experience high voltage, therefore I would need high dielectric breakdown for this material. I was wondering if you have a service for dielectric coating on ITO glasses.
Reference #276257 for specs and pricing.